Glass Beads
Glass beads are used predominantly in two different product constructions: Engineering Grade (EG) beaded sheeting, and High Intensity (HI) beaded sheeting.
EG structures are the most simple and work similarly to what we discussed in Chapter 2.
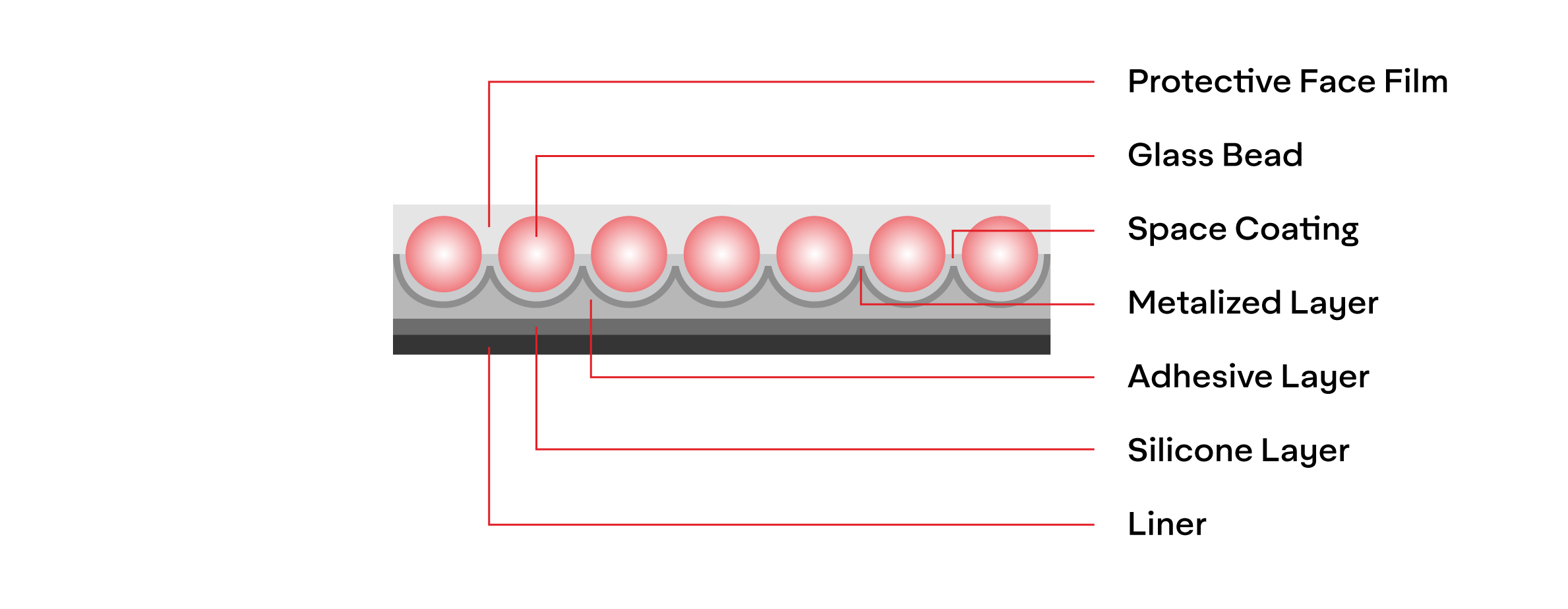
This construction is typically used when some retroreflectivity is required, but it’s secondary to other factors like cost, or, in some cases, flexibility or conformability. Because of its simple construction, EG sheeting is fairly robust, especially for the cost. Typical applications could include license plates where there is plenty of light from headlights, utility applications, or parking signs and signs for pedestrians, where you may not want to distract drivers with a bright sign. In the US, the Federal Highway Administration (FHWA) does not allow EG sheeting to be used for traffic applications.